Add automation seamlessly to any or all of your end-of-line processes.
Streamlining your end-of-line product transfer increases efficiency, profitability and reliability. Cobot technology can be introduced swiftly to specific stages of the line, either complementing or replacing human handling.
Palletising
Palletising your packed product is a prime area for automation, and can be made fast, reliable and hassle-free.
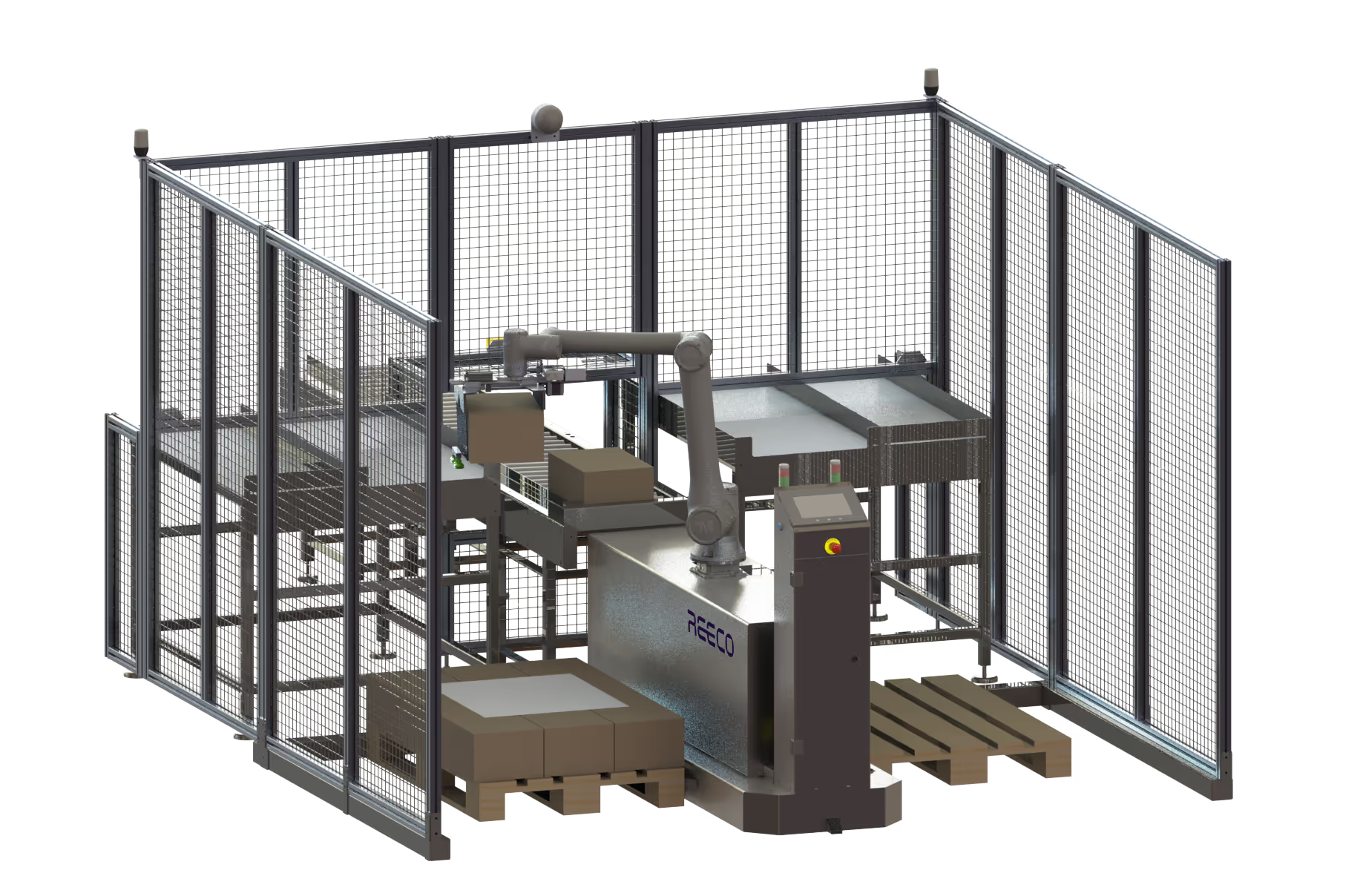
Autonomous transport (AMR)
Our range of centrally managed OMRON Autonomous Mobile Robots (AMRs) range in payload capability from 60 to 1500kg. AMRs safely navigate autonomously, transporting loaded pallets from palletiser to dispatch.
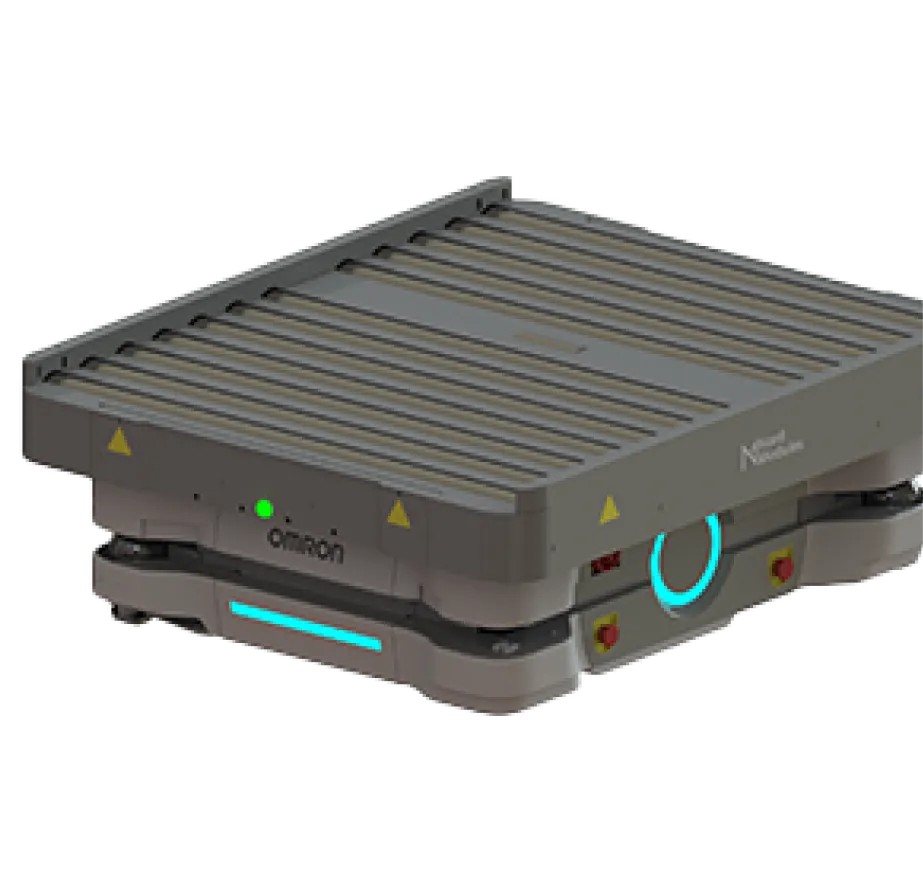
Bowl
feeders
Bowl feeders automate the precise feeding of components in pick-and-place cell operations. They ensure a continuous supply of correctly oriented parts, ready for the next stage of the manufacturing process.
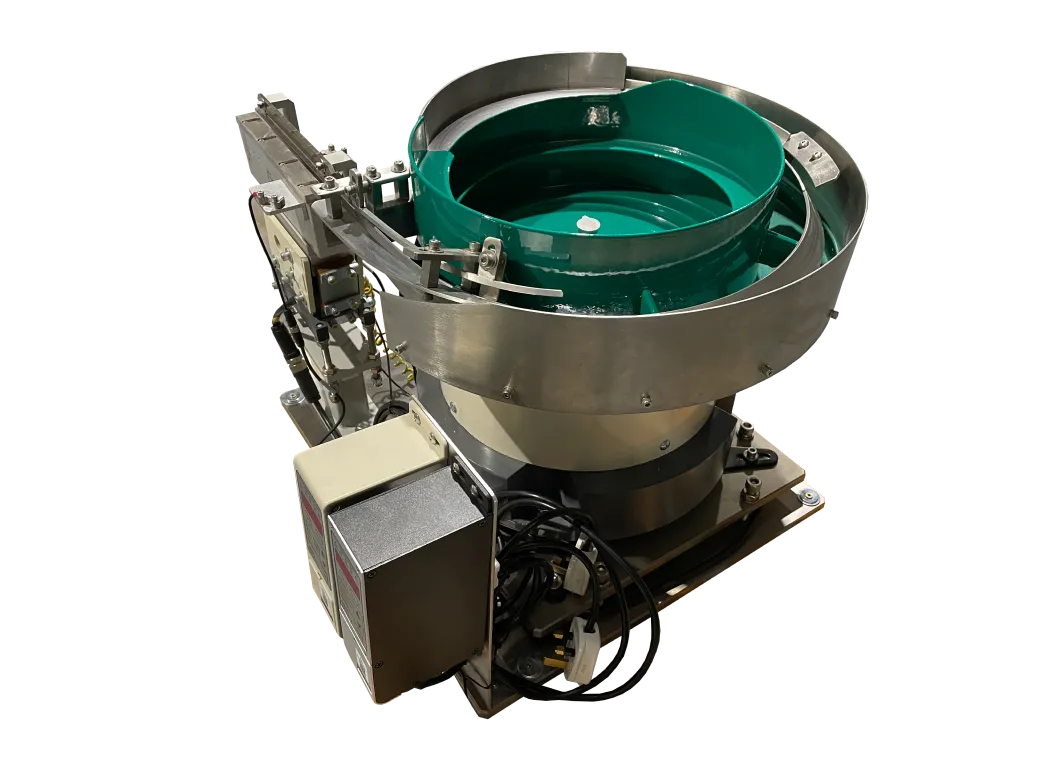
Case and tray
packing
Our OMRON TM14-equipped case packers integrate seamlessly with your existing facility, reliably packing boxes and trays at speeds of up to 1200/hr. The Reeco CP range reduces manual labour and handles payloads of up to 14kg.
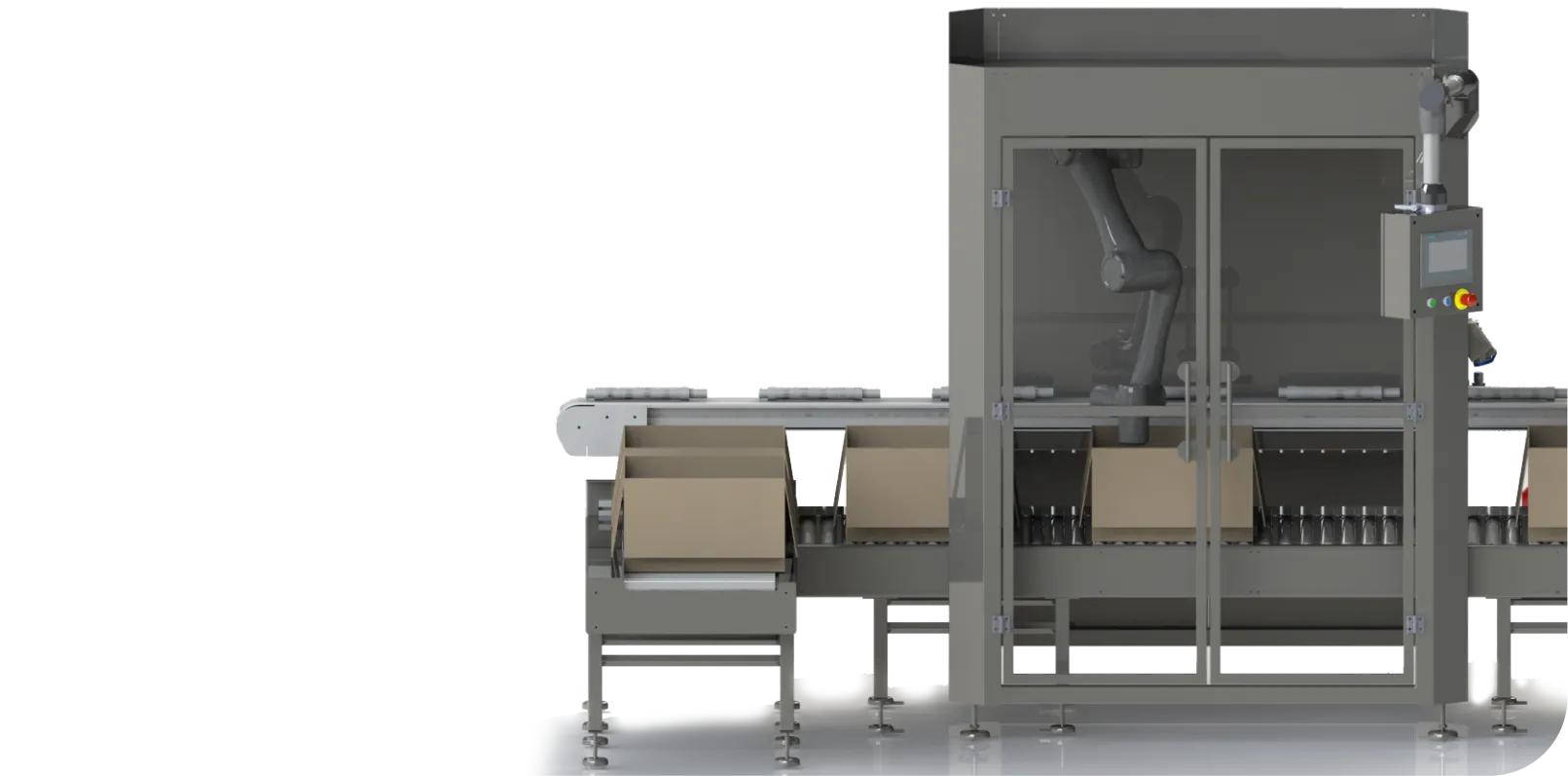
Conveyors
A key part of any production line, our highly customisable conveyors connect various stages of your packaging processes and are designed to integrate seamlessly with your existing equipment.
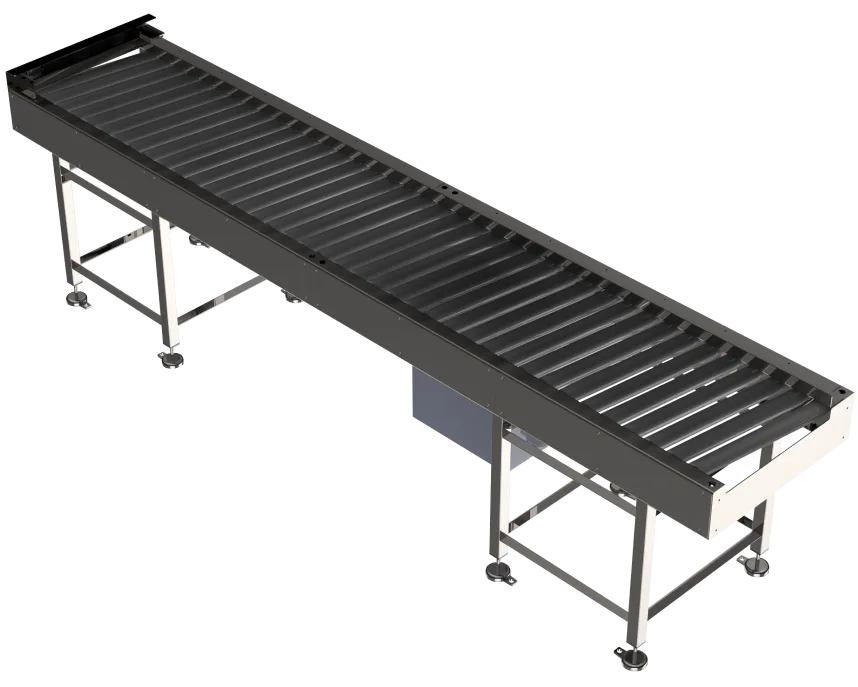
Case
erecting
Automatic case erectors enhance the packing process by producing reliably square boxes, improving product protection, and ensuring palletising processes are simplified.
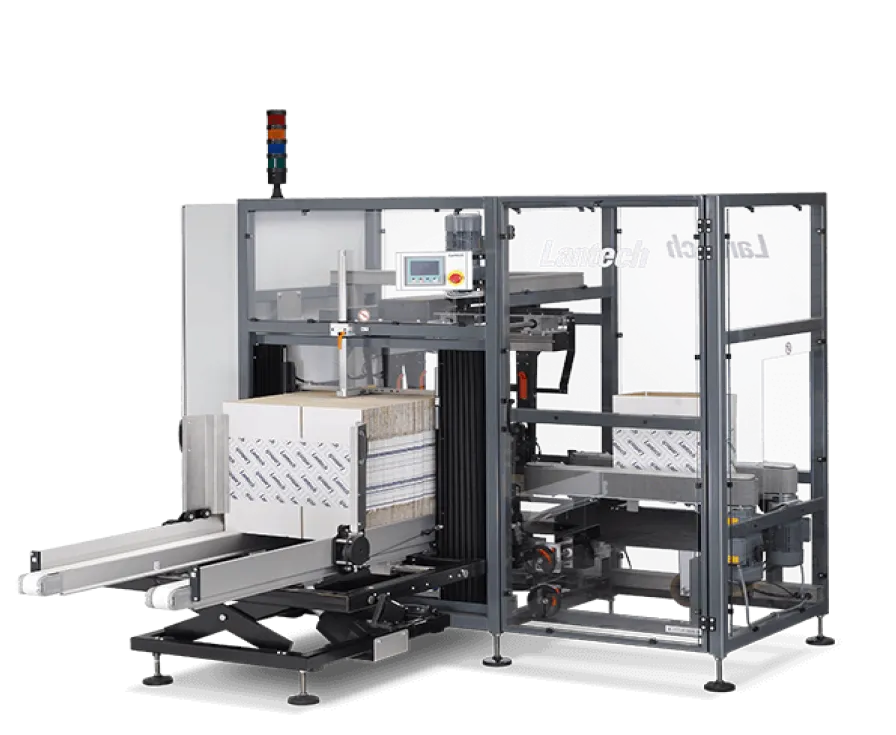
Case
sealing
Automate the process of folding and sealing packed boxes with our range of case sealers.
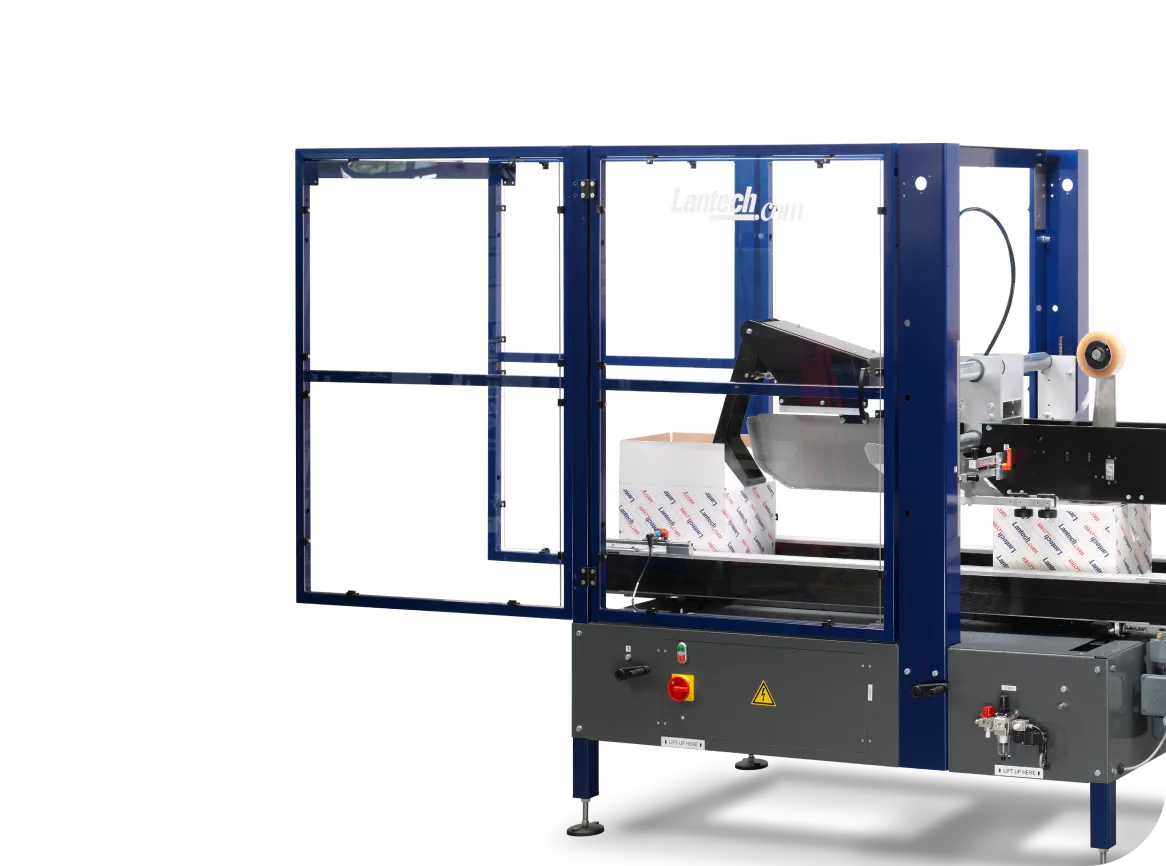