How the RB1200 Cobot Palletiser Can Simplify Your Automation Deployment
Greater automation and collaborative robotics (cobots) are the future for many industries, including logistics. Research by BMW found humans and robots work more than well together. In fact, human-robot teams were 85% more productive than working alone. It makes sense. Combining the speed and accuracy of robotics with the flexibility and intuition of humans compounds the benefits from each to build an unbeatable team.
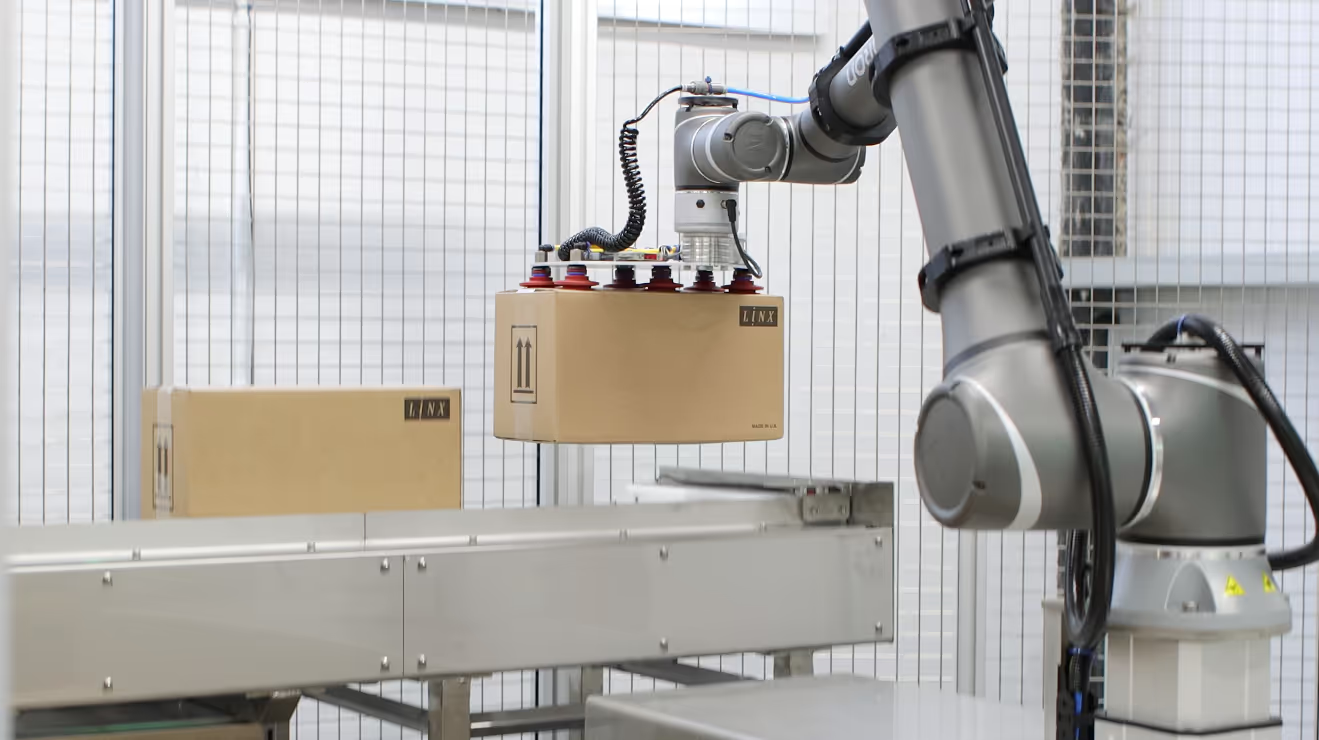
With the RB1200 Cobot Palletiser, Reeco, in collaboration with OMRON, is bringing a revolutionary new approach to end of line palletising. Creating an easy, flexible, safe, and compact solution to getting stock palletised and ready for transport.
Palletising is a task perfectly suited to automation. The simple yet repetitive and physically demanding process of getting goods stacked leads to complications when performed manually. In 2019/2020, the Health and Safety Executive (HSE) estimated 19% of non-fatal workplace injuries were caused by handling, lifting, and carrying.
Plus, given the labour shortages facing the UK and the wider world and the potential for spiralling staff costs, now is the ideal time to get your company less reliant on manual labour.
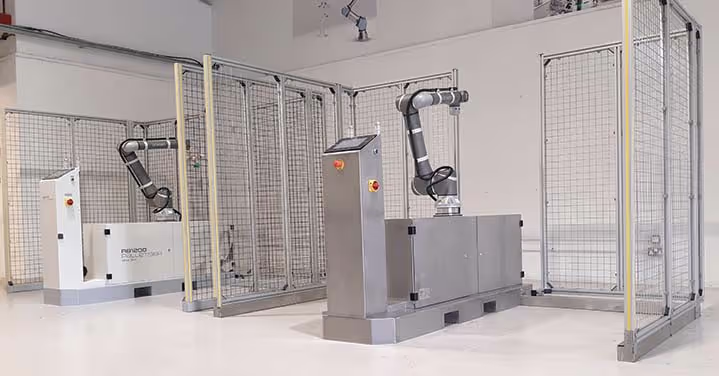
While there are plenty of benefits to automating your palletising processes (greater output and accuracy, reduced labour and operational costs, etc.), its implementation also has challenges.
However, with the RB1200 Cobot Palletiser, humans can collaborate with robotics on their terms, implementing a solution that fits their specific needs.
The Challenges of Robotic Palletiser Implementation
Space Requirements
Most robotic palletisers are large, bulky systems that take up significant space in an environment where it is at a premium. Space requirements in factories and warehouses, especially during end-of-line processes, is an important challenge in robotic palletiser implementation.
However, at 2.2m x 3.2m, the RB1200 is designed for small footprint installations. Giving facilities the benefits of robotic palletising without taking up too much space and restricting other operations.
Safety Concerns
Overall, robotic palletisers positively impact the safety of employees, removing a significant cause of RSIs and more severe injuries. However, they do introduce new machinery into the workplace, presenting a different kind of risk.
Palletisers must be installed and appropriately secured, plus staff have to be adequately trained to ensure safe use. They require significant safety considerations through fencing and light guards, which can increase the space palletisers use.
Each RB1200 system comes with fully-integrated safety features for quick deployment and compliance. This includes safety fencing for each pallet runway restricting and monitoring entry points through the use of safety scanners.
System Design
Software design for robotic palletisers is often based on complex programming languages that require costly and time-consuming training to master.
OMRON’s collaborative robots come with the TMFlow software package, making them easy to use without sacrificing their capabilities. TMFlow’s intuitive interface makes software design quick and simple while interfacing seamlessly with the RB1200’s EasyStack Visual Software.
Plus, with the offline editor, you have the flexibility to create and modify programs without being connected to the palletiser. Work on your software design where and whenever suits you best.
Flexibility
Many automated palletiser systems are inflexible and designed for only a specific task. As a result, they may require significant downtime to change functionality, adjust to new pallet layouts, or redeploy to new lines.
With Reeco’s Easy Stack Visual software, the RB1200 is designed to be flexible and maximise utilisation. The interface with easy to understand visual aids allows you to programme new pallet formats quickly. Configuration takes a few steps with only basic pallet/ box parameters and layer design/stack preference inputs required.
Easy Stack reduces the changeover time for palletiser applications keeping your business moving and more profitable. The tool is designed for use by line operators without the need for engineering support. Plus, the plug and play palletiser can be redeployed between lines quickly to meet your facilities demands.
RB1200 Cobot Palletiser
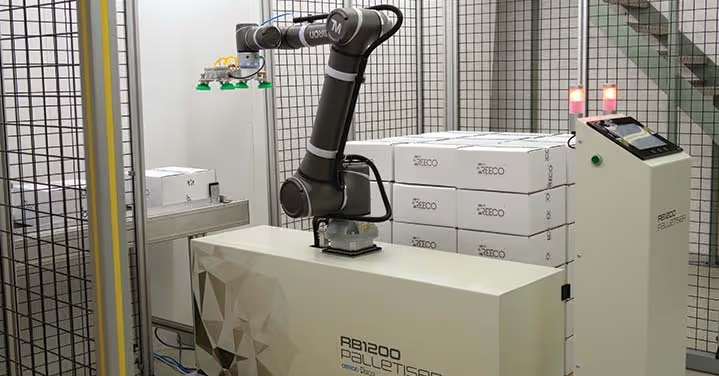
At first glance, the hurdles to implementing robotic palletisers may seem too great. But with Omron and Reeco’s RB1200 Cobot Palletiser, you can clear them with room to spare and get an automation solution that takes your facility to new heights
- Compact size reduces footprint required for operation
- comprehensive safety features allow for quick and compliant deployment
- Software design based on an intuitive and easy to learn interface
- Flexible use that works no matter the application, reducing downtime and maximising utilisation
The RB1200 offers a best-in-class palletising solution no matter your facilities requirements. With a pick rate of 12 cycles per minute and the ability to handle products up to 10kg, the RB1200 ensures greater throughput for your business. In some situations and with a reduced pick rate, payloads of up to 12kg are possible. Plus, all this comes with a lower price, saving up to 50% compared to traditional robotic palletiser systems.
Learn more about the RB1200 today and discover the benefits of automating processes at your facility.
You may also be interested in
Centralised vs localised palletising: Which is best for the end of my production lines?
The move towards end-of-line automation has been accelerated by changes in the labour market post-Brexit. The reduced access to overseas workers has resulted in a smaller pool of manpower and rises in the statutory minimum wage has also increased the cost of labour. This has all added to the existing arguments of enhanced productivity and reliability for switching to automated processes.
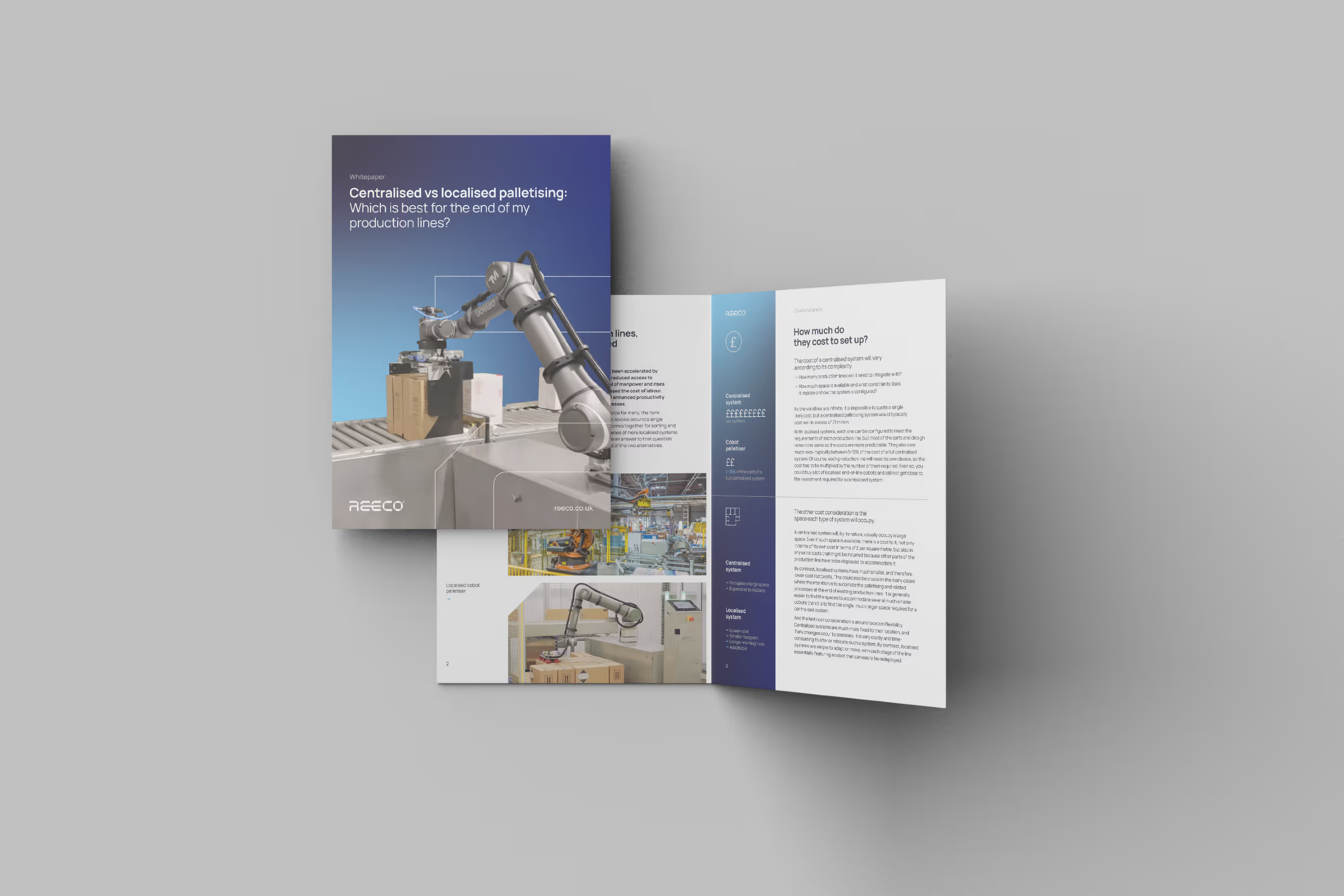