Reeco delivers bespoke automated fulfilment solution to Butternut Box
Reeco has recently successfully delivered a fully customised depalletising and product transfer solution to meet fulfilment needs at fresh dog food company Butternut Box. The implementation of an automated product handling system has helped the growing brand to upscale its capabilities and improve efficiency at its new fulfilment facility.The new solution has also significantly reduced the need for manual handling and enabled the redeployment of staff members onto higher-skilled processes along the fulfilment line...
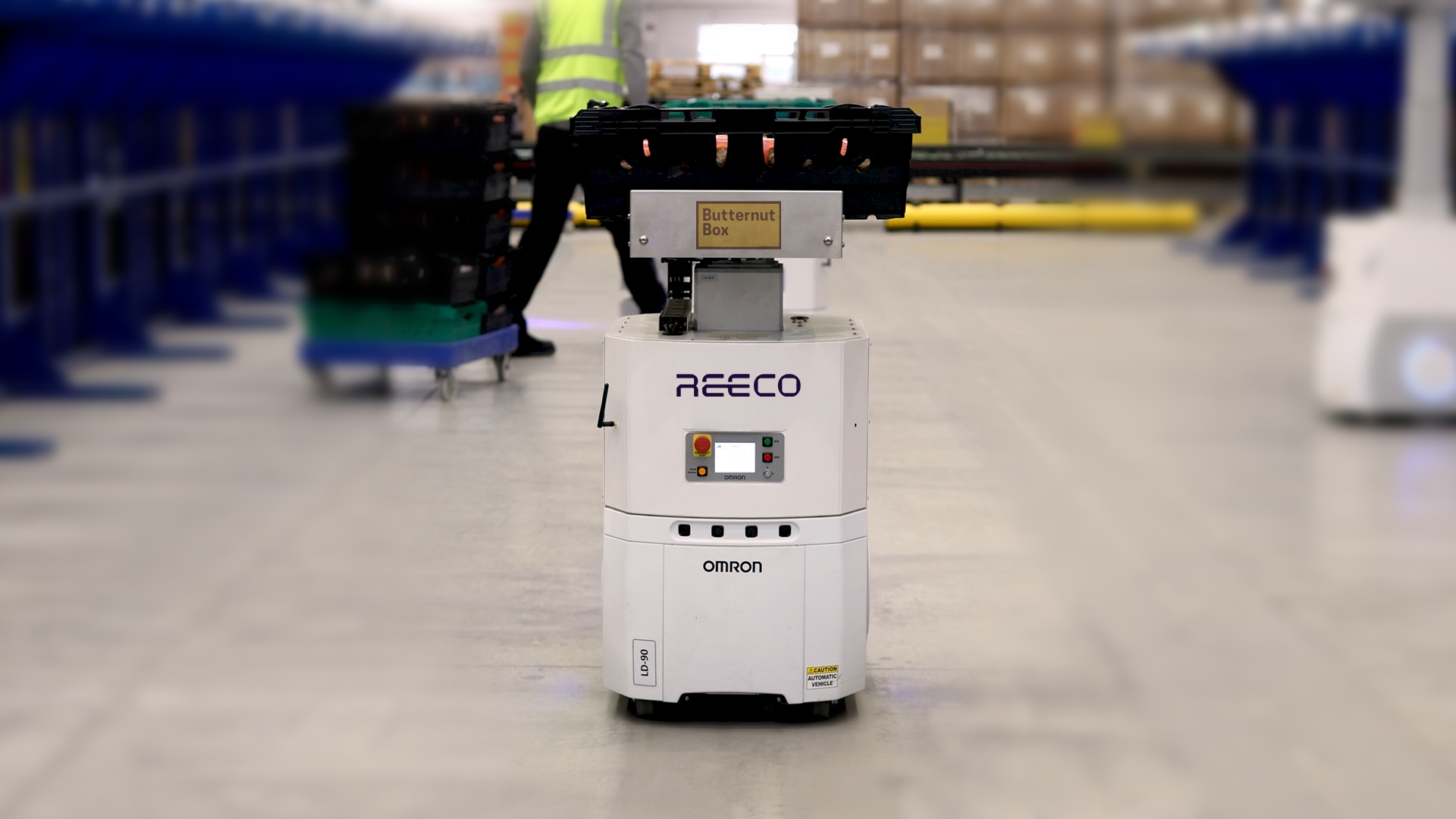
End-of-line efficiencies to support growth
Butternut Box is the go-to subscription service for high-quality fresh food for dogs. They wanted to increase throughput and optimise end-of-line efficiencies both to meet increasing demand and to plan for future growth in a scalable, modular way. The Reeco design team rose to the challenge, designing a bespoke system that could handle goods movements taking place partially inside a freezer, as well as transfer products from conveyors at different heights. Critically, of course, the full system also needed to work safely and efficiently alongside fulfilment staff.
"Reeco has been a brilliant partner, working closely with us through the entire process right from design, through to installation and maintenance. They’ve delivered an excellent localised automation solution, which puts us in an excellent position for future growth in a modular fashion."
A truly bespoke solution
At the start of the production line, six Reeco RB2000 depalletisers unload crates of fresh dog food, which are then transported via a fleet of 18 OMRON AMRs to fulfilment stations, where operators pack unique customer orders.
The AMRs feature custom top modules from one of Reeco’s integration partners, Dimalog, which allow product collection and delivery between different line heights. The fleet is managed via a single interface and is integrated with an on-site ERP system to manage product demand and delivery. For orders heading to mainland Europe, a Reeco RB2000 palletiser with EasyStack software is used to transfer goods onto Euro pallets ready for shipping.
The design team at Reeco worked in close conjunction with Butternut Box to create an optimised layout and system design across critical stages in the fulfilment line. They used detailed CAD drawings to map out the AMR area, including calculating distances and heights in order to simulate and verify the desired movement of goods. This was followed by physical testing using the initial simulation overlaid on the physical layout of the production environment to create an optimal plan for reliable AMR traffic movement.
The localised automation supplier of choice
The project is a perfect example of how the successful deployment of cutting-edge AMR technology can make a very real difference to operational excellence.
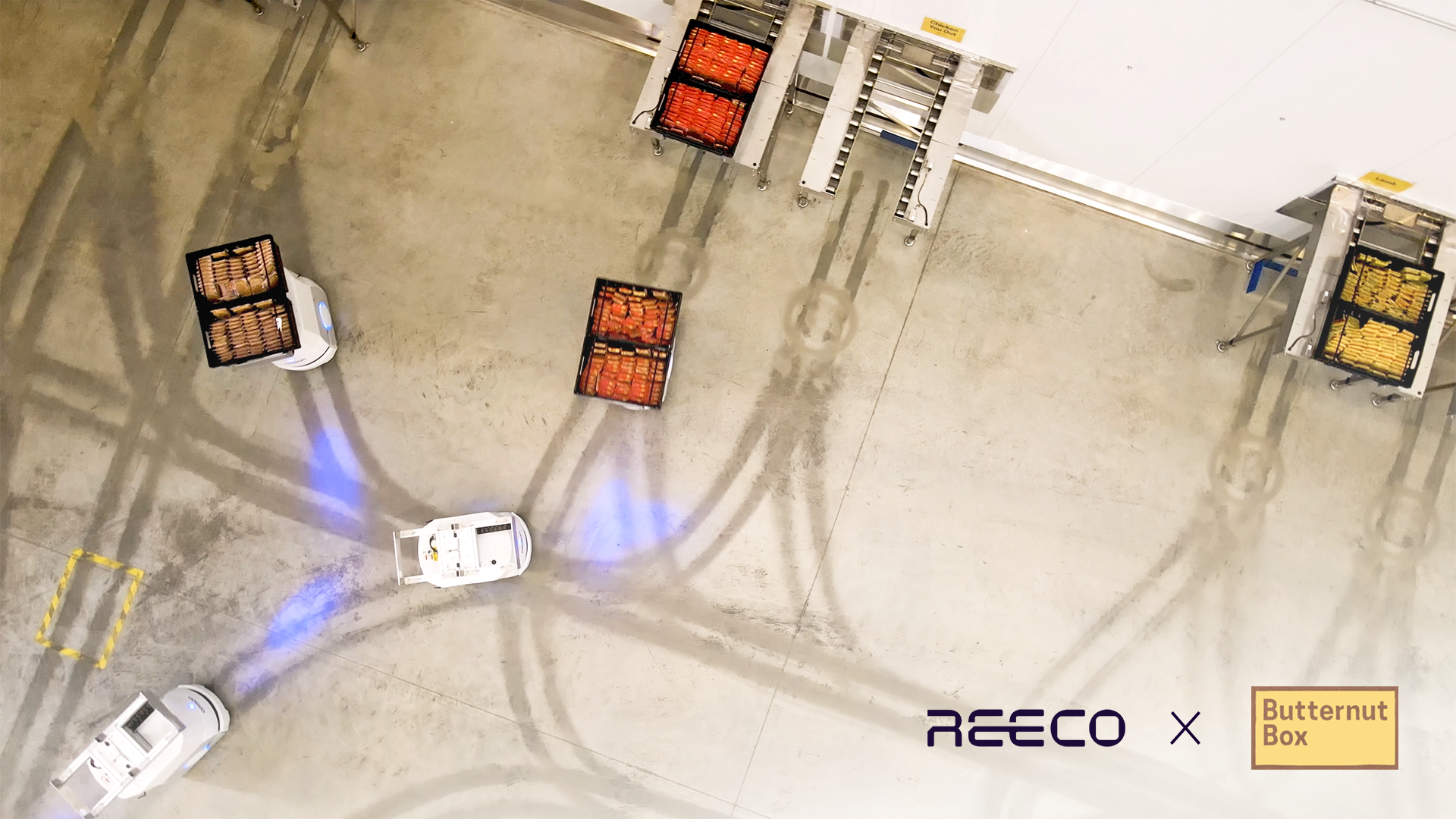
You may also be interested in
We’re Hiring: Multi-Skilled Engineer (Electrical Bias)
Reeco Automation is on the lookout for a Multi-Skilled Engineer with an electrical bias to join our growing team. As demand for our automation solutions increases across the UK and overseas, we’re expanding our workforce to meet new challenges.
.png)