What is a palletiser
A Palletizer is an automated machine which stacks products, such as cartons, trays, bottles and bags onto pallets. Typically used by manufacturers who produce in large volumes.
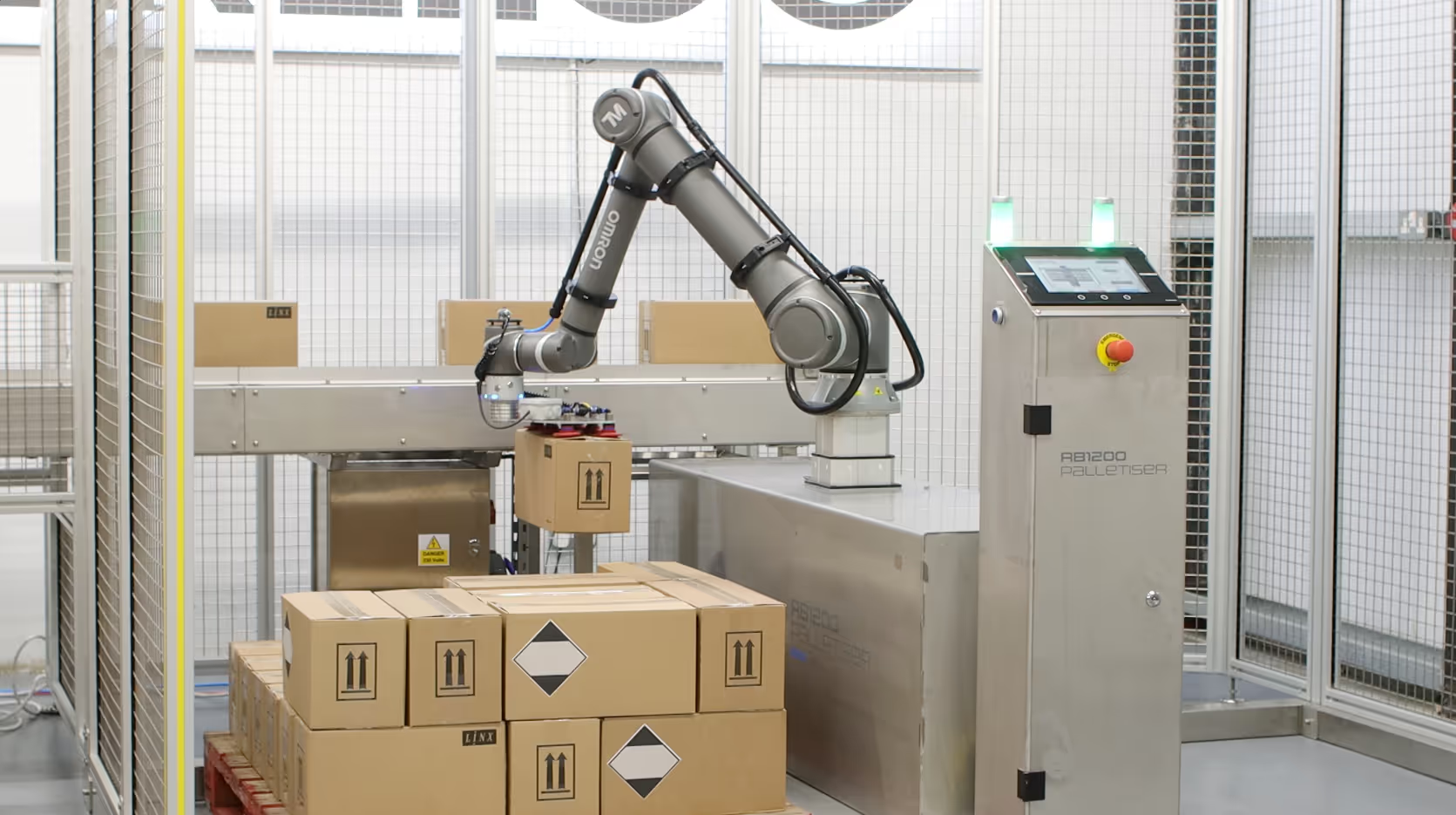
Palletizing is a necessary evil, it doesn’t add value to the end product but also requires time and attention in order to get product out the door. Palletizing is a very manual process as operators need to continuously move payloads from A to B, resulting in staffing issues, injury and inconsistency.
Because of this, our robotic palletizing system are a staple of manufacturing automation, their use is often seen as an investment in future cost reduction, typically paying for themselves in 1-2 years.
They are also a means of providing workforces with more fulfilling and less physically demanding jobs which instead require human thought and dexterity, leading to higher staff retention, less injury and better overall efficiency.

What can they Palletize?
Palletizers are mainly used by manufacturers, but what are they capable of handling? Well, palletizers come in all shapes and sizes, but if you currently put products on a pallet, there will be an appropriate palletizer which can automate that process.
Some examples include:
- Taped box
- Glued box
- Hooded Box
- Shelf-ready Packaging (perforated boxes)
- Open Top Box
- Wrapped Product
- Collapsible Trays
- Bale Arm Trays
- Bottles
- Drums
- Bags
Why is Palletizing Products Important?
Palletizing is a process which has existed for over 100 years, continuing to support logistics infrastructure to this day.
The concept of ‘Unit Load’ states that its quicker and more economical to move lots of items rather than one at a time, so the more product handled in one go, the lower the cost.
Unit load implies that materials should be handled in the most efficient way, reducing the number of movements needed for a given amount of material.
There are many types of unit load, with pallets being one of them. Pallets are essentially a portable platform which can be easily lifted, moved and decanted. They are a staple in manufacturing, and important for efficient logistics operations, internally and externally.

What Types of Palletizer are there?
Producers and manufacturers in all industries need efficient logistics systems in place to move goods.
Pallets are a universally accepted method, they are versatile, efficient, come in different shapes and sizes and generally accommodate most products.
The Palletizer market has developed to accommodate most palletized loads, ranging from robotic cells to manual and semi-automatic systems.
Manual Palletiser
Manual Palletizers act as an aid to operators, making the palletizing process less intensive and reduce risk of injury.
Manual Palletizers generally have a pallet lift which operators adjust based on the current layer, positioning the pallet at an ergonomic height for the operator to continue stacking.
Semi-Automatic Palletiser
Semi-automatic Palletizers are the next step up from manual, offering some automation, but also requiring operator input.
Semi-automatic systems will typically require an operator to orientate and push products onto a palletizer platform, the palletizer will then place these products onto the pallet automatically.
High Level Systems
High level palletizers are elevated systems, products make their way to the top and are stacked layer by layer, the pallet lowers on a lift with each completed layer. High-level palletizers can be either automated or semi-automatic.
For automated systems, conveyors and pushers locate boxes and push them onto a platform, the platform will then transfer the completed layer onto the pallet.
Low Level Systems
Low-level Palletizers stack product on a ground level, so instead of lowering the pallet like high-level palletizer machines, a low-level palletizer will lift layers of product and place them on top of the pallet.
Similar to high-level, automated low-level systems will use conveyors and pushers to locate and orientate product, pushing them onto a platform before the platform transfers them onto a pallet.
In-Line Palletizers
In-line palletizers use a continuous motion to guide and orientate products into rows, forming their position on a layer forming platform.
This is done until the layer is complete which is then placed on a pallet.
Robotic Palletizers
Robotic Palletizers utilise robotic arm with some form of gripper to pick and place product. There are a few different versions of a palletizing robot, each with varied flexibility and movement.
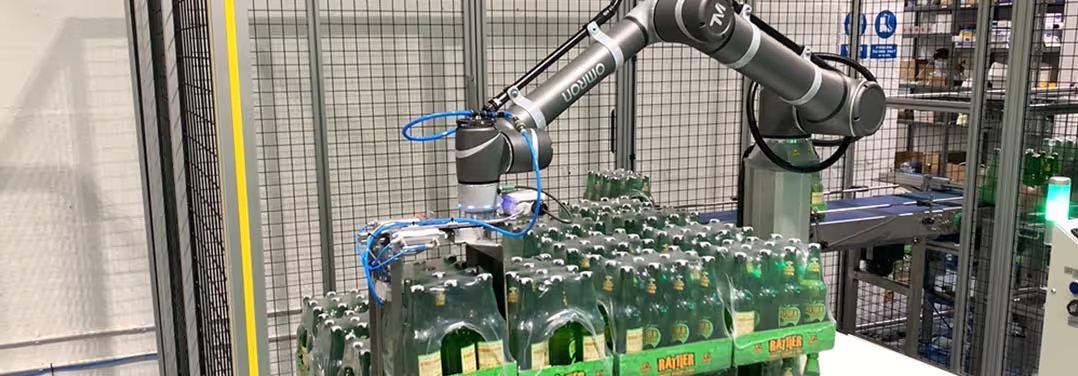
Cartesian Robots
Cartesian Palletizers are simple ‘pick and place’ palletizers, consisting of metal frames and a telescopic lifter, usually operated by servo motors.
Cartesian Palletizers are simplistic in nature, operating on 3 axis and typically used for products which are consistent in weight and size.
Cartesian palletizers have high payloads, but offer comparatively low throughput speeds.
Gantry Robots
Gantry palletizers are a series of frames and rails which are used to transport loads from A to B.
Gantry palletizers are also referred to as cartesian palletizers since their movement is similar, although they’re generally slower, bigger and capable of lifting heavier loads.
SCARA Robots
Selective Compliance Assembly Robot Arm’s (SCARA) operate on 4 axes, and typically capable of large payloads.
They are much quicker than Gantry or Cartesian Palletizers but operate like industrial robots.
SCARA Palletizers use a lifting column which lifts and rotates the SCARA Robot, giving it full reach across pallets and conveyors.
Industrial Robot Palletizer
Industrial, or articulated Palletizers, are the next step up in flexibility.
Industrial Robots have more degrees of freedom which allows them to manipulate and handle product in more configurations.
Industrial robots are also quicker and offer large payload capabilities, however they demand large amounts of floor space.
Collaborative Robot Palletizer
Collaborative Robot (Cobot) Palletizers are flexible palletizers which are designed to operate in close proximity to workers.
They offer the same movement flexibility as industrial robots, but with reduced footprint and lower payload.
Cobot palletizers generally offer 10-12 picks per minute with payloads of 10-25kg.
What are the reasons for using a Palletizer?
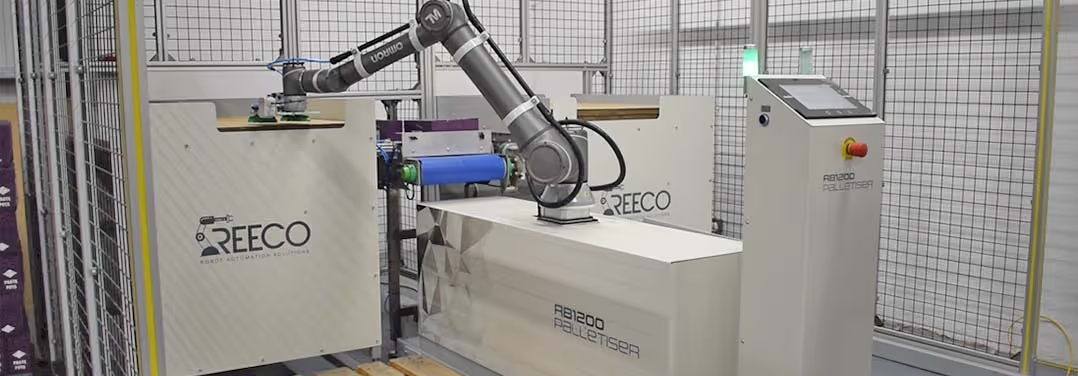
Palletizers have been around for decades, they are a staple within automation due to the benefits that tag along with them.
Stacking pallets is a laboursome job, its manually intensive and requires consistent resources in order to satisfy production and logistics requirements.
There are many reasons why a business may choose to automate the process with a palletizer, here are a few:
Labour Challenges
Challenges of labour are one of the biggest drivers in automation. In recent times we are experiencing amplified effects of this due to Covid and other economic hurdles, these challenges are driving companies toward change and streamlining processes to reduce costs.

Rising Cost of Labour
Labour is becoming more expensive. While a strong labour force is crucial to business performance, certain tasks such as palletizing, which add no value to the end product are a necessary expense to distributing manufactured goods.
While hand palletizing is usually the first and most logical option, as companies begin to scale this, non-value-added expense also increases.
Introducing an automated system, like a palletizer machine, allows companies to invest in onsite equipment opposed to sinking large costs into labour.
Typically paying for themselves in 1-2 years, palletizers are an investment into future cost reduction and operational bonuses.
Labour Shortage
There is a huge shortage of labour in the UK. While hand palletizing may be preferred by some manufacturers, obtaining the labour to begin with is proving to be difficult.
According to the Food & Drink Federation Since the start of the pandemic its estimated that there are 1.1m fewer people in the labour force. In the manufacturing industry there were 97,000 vacancies in January 2022, an increase of 113% on the year and 80% compared to two years ago.
Staff Turnaround
Keeping hold of valuable workers is proving to be more difficult than it previously was.
Across warehousing there is a 46.1% staff turnover rate, compared to the 12-15% average across the board for other sectors.
This is likely to cause operational inconsistencies and require attention to maintain and manage, some manufacturers may resort to agency workers which come at a premium.
Repetitive Strain Injury
Manual handling places considerable strain on employees. Handling, lifting, carrying and arranging inventory increases the risk of Repetitive Strain Injury (RSI) while also having the potential of severe accidents.
Palletizing products is a repetitive process which leaves employees susceptible to RSI’s, according to the Labour Force Survey, there are over 200,000 work-related RSIs in the UK every year.
The Health and Safety Executive (HSE) estimate 639,000 workers sustained a non-fatal injury in 2019/2020, of which 19% (131,700) were caused by handling, lifting and carrying. An increase of over 13% from the year before.
Return on Investment
Palletizers are an investment in future cost reduction, they typically work with a high operating equipment effectiveness (OEE) as they are an integral part of production, therefore running most of the time.
When compared to manual labour, a palletizer will typically pay for itself over a 1-2 year period, allowing businesses to ride the benefits of automation right into the green.
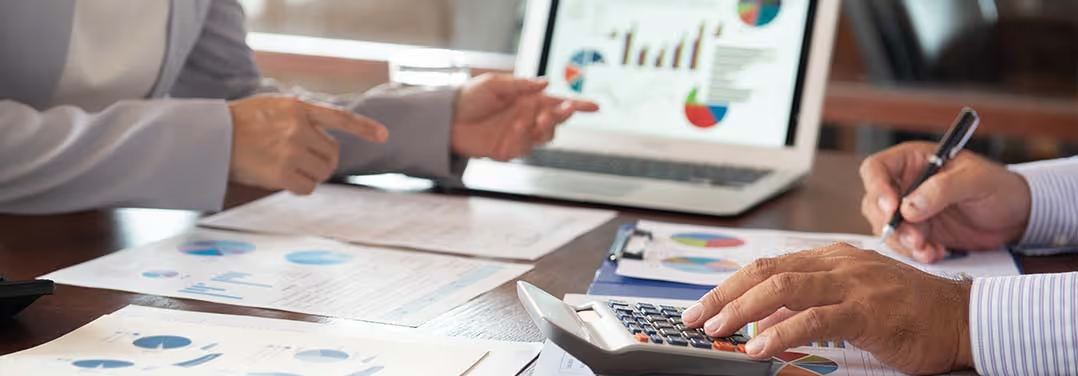
Throughput: Manual Palletizing vs Automatic Palletizer
Manual palletizer operator is labour intensive, a limited labour force is likely to generate diminishing returns when production ramps up due to fatigue and potential injury, this can lead to slower and less accurate performance.
An automated palletizer is versatile and reliable, enabling businesses to maximise throughput without concern. They provide measurable and repeatable outputs which can be scaled up or down to suit requirements, giving manufacturers complete control over operations and output levels.
Stacking Strength & Damaged Loads
Inconsistences with manual labour can often lead to damaged goods, usually a result of fatigue or RSI’s which reduces care of handling. Damaged products lead to costly product returns, studies have found that the cost of replacing damaged products can be up to 17% higher than the original shipping cost.
Damaged goods are not only an immediate cost but could have long term ramifications too. One study found that 58% of people say their relationship with a business or supplier would be negatively impacted if they received a damaged product. Moreover, of that 58%, 20% would go as far as to never do business with that company again, even if it’s the first time its happened.
Uptime
Most automation systems offer uptime benefits due to their ability to work around the clock, palletizers are no different. Unaffected by sickness, injury, breaks and holidays, palletizers are a reliable means to automating at the end of your production line, allowing manufacturers to do more in the same amount of time.
_
Interested in Talking to a Reeco Specialist?
Reeco is a system integrator of automation equipment, specialising in Collaborative Robots (Cobots) & Autonomous Mobile Robots (AMRs). Supplying both SME’s and some of largest blue chip companies throughout the UK, Reeco have designed and installed solutions to suit all types of industries and applications.
You may also be interested in
Centralised vs localised palletising: Which is best for the end of my production lines?
The move towards end-of-line automation has been accelerated by changes in the labour market post-Brexit. The reduced access to overseas workers has resulted in a smaller pool of manpower and rises in the statutory minimum wage has also increased the cost of labour. This has all added to the existing arguments of enhanced productivity and reliability for switching to automated processes.
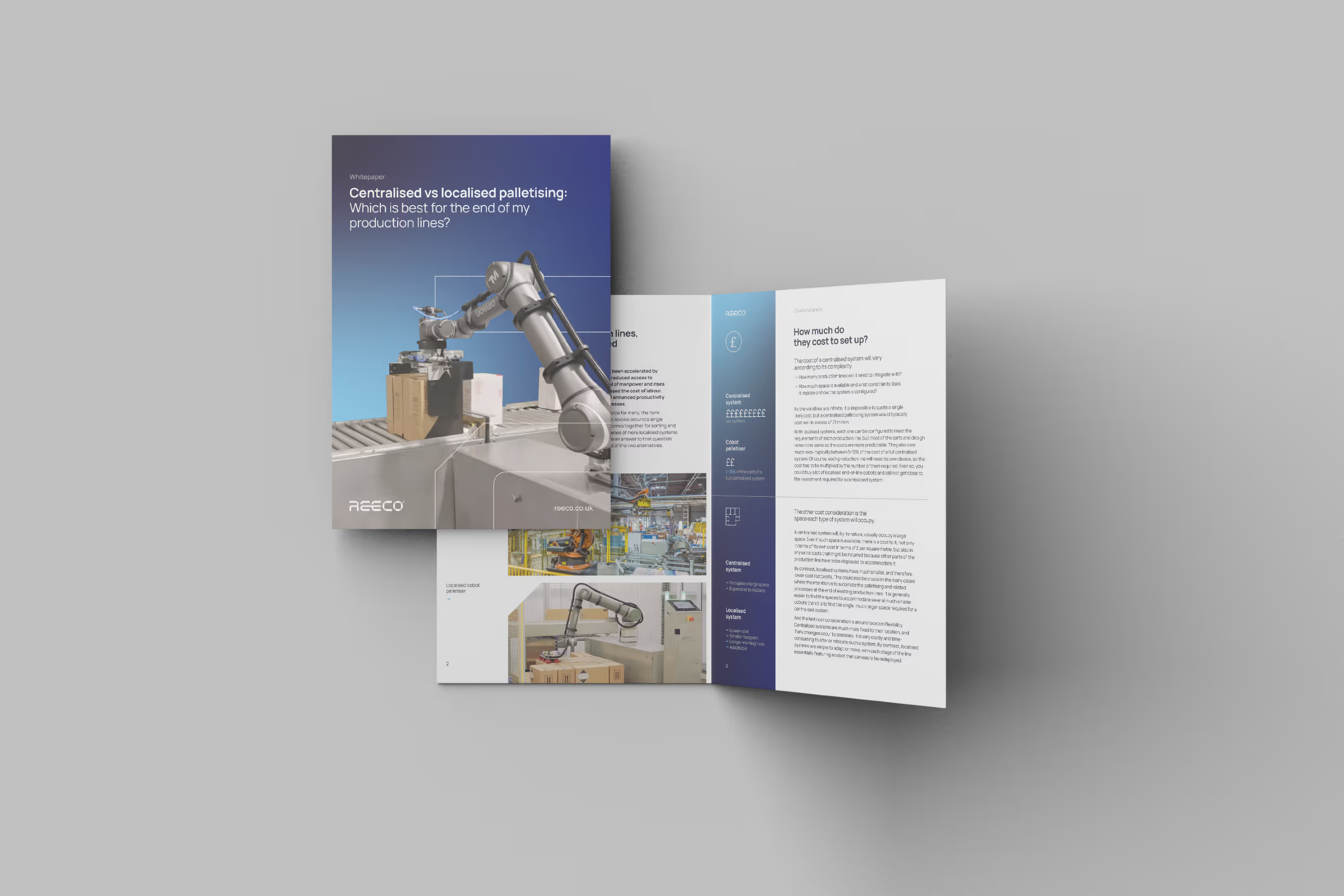