News
The latest news from Reeco and the wider world of automation. From new tech applications and innovations, to cobot industry success stories, and more.
Reeco’s newest palletising system, the RB Lite Palletiser, is designed for manufacturers looking to automate smarter, without the scale, cost, or complexity of a full-sized cell.
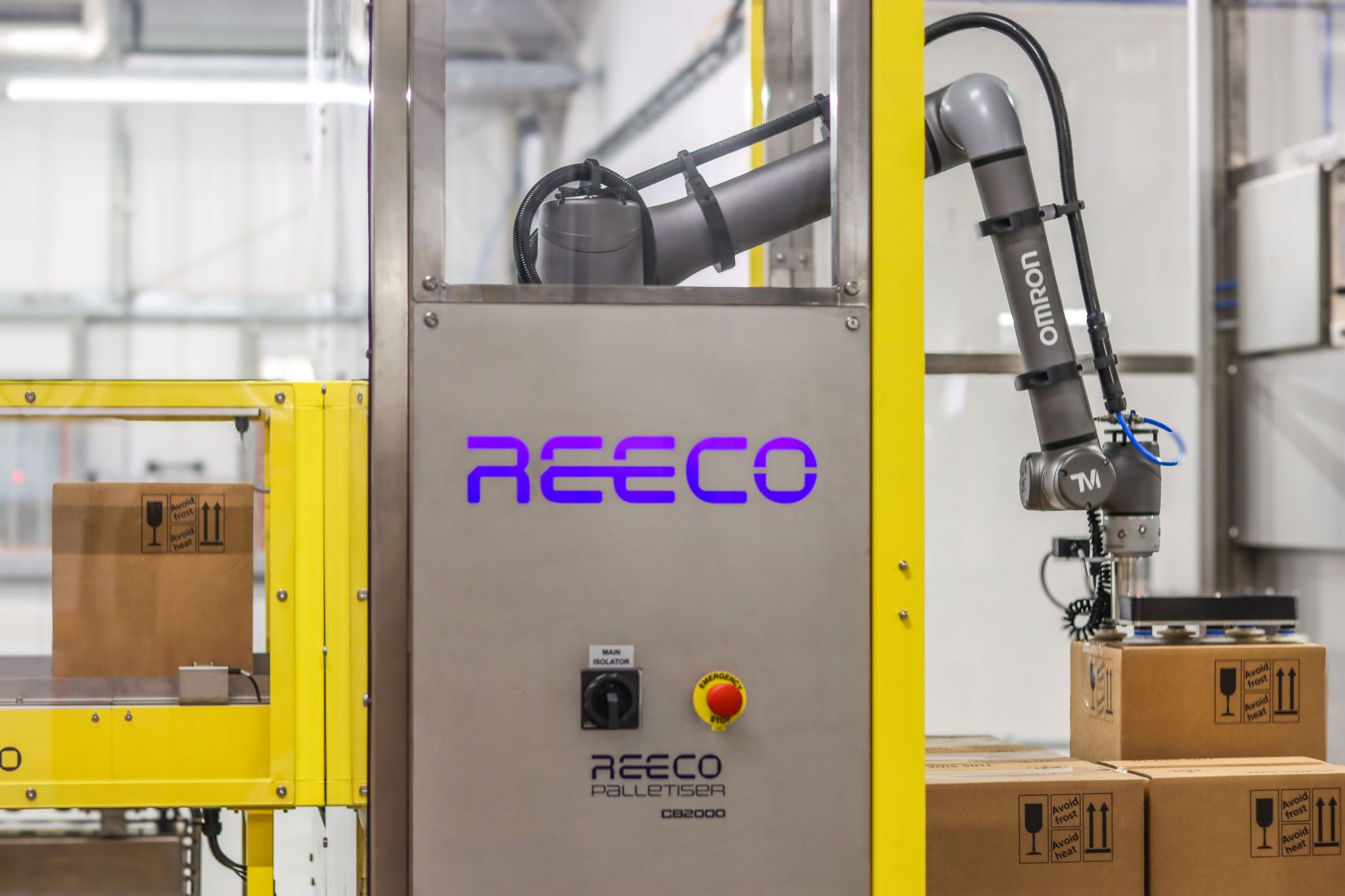
The CB2000 is the latest addition to Reeco’s palletising portfolio, a compact, floor-saving solution designed to bring automated palletising to even the smallest of production lines.
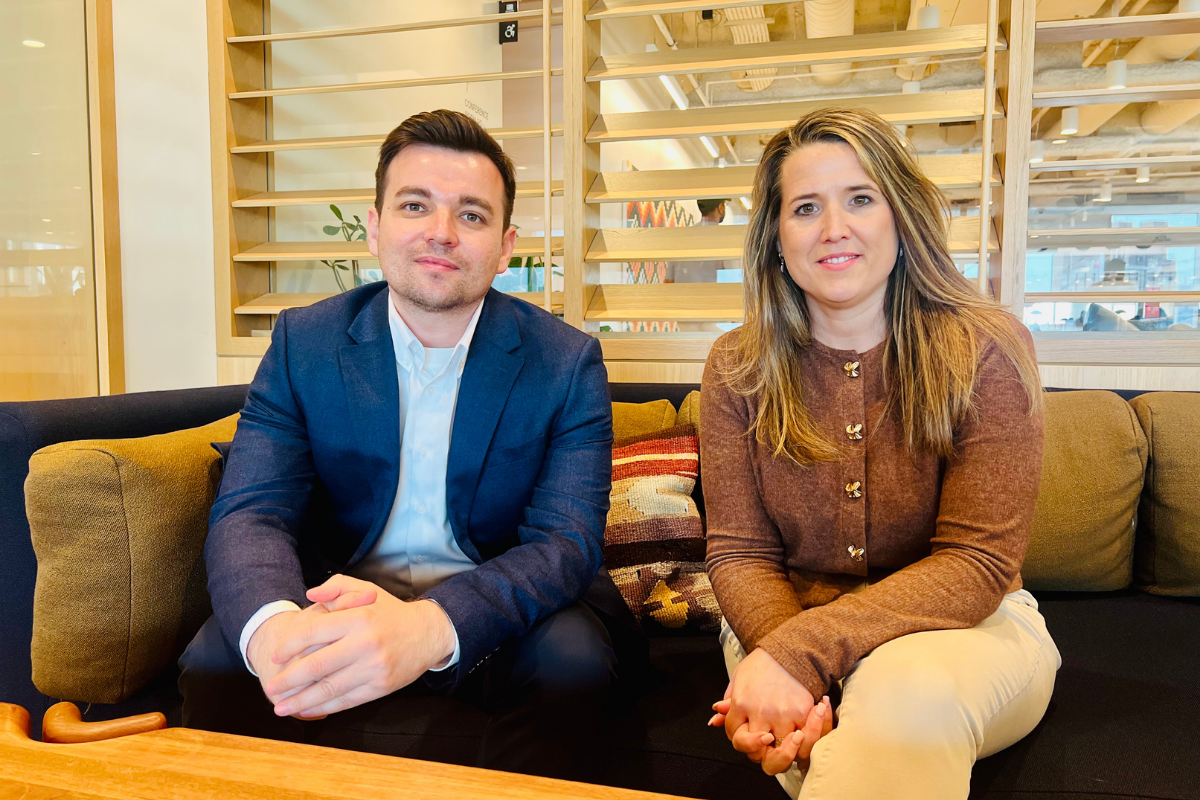
Robominder, a pioneering AI software company transforming robotics operations through intelligent automation, is pleased to announce the appointment of Rosie Davies, Managing Director of Reeco Automation, to its Board of Advisors.
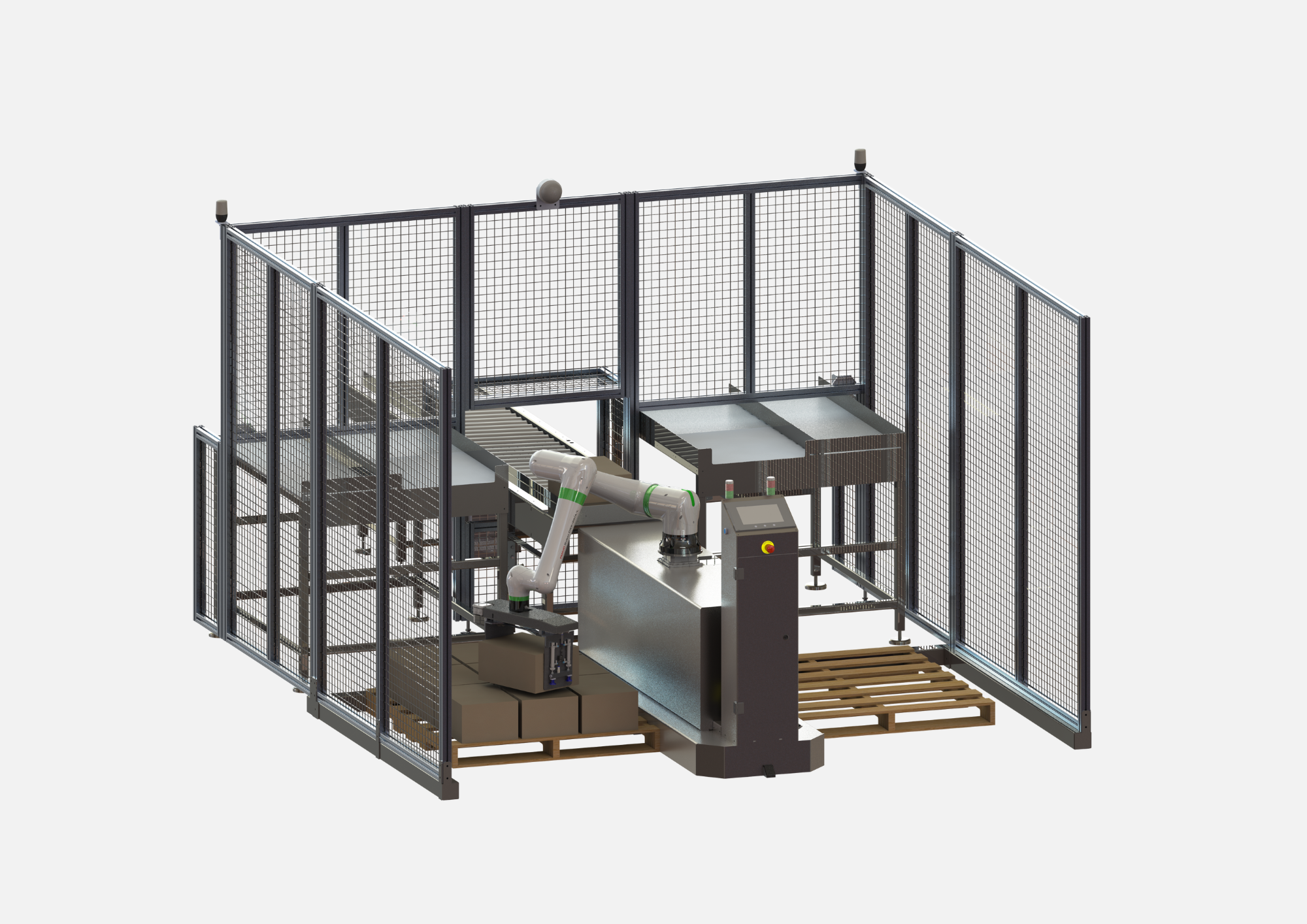
As manual loading becomes an increasingly harder role to recruit, Reeco’s automated end-of-line RB Palletiser systems have grown in popularity, particularly among food & beverage producers. By extending the RB portfolio to incorporate FANUC’s CRX 20 and 30 models, both companies are confident that more manufacturers – including SMEs – can now enjoy the efficiency gains, energy wins and cost-saving benefits that automation delivers.
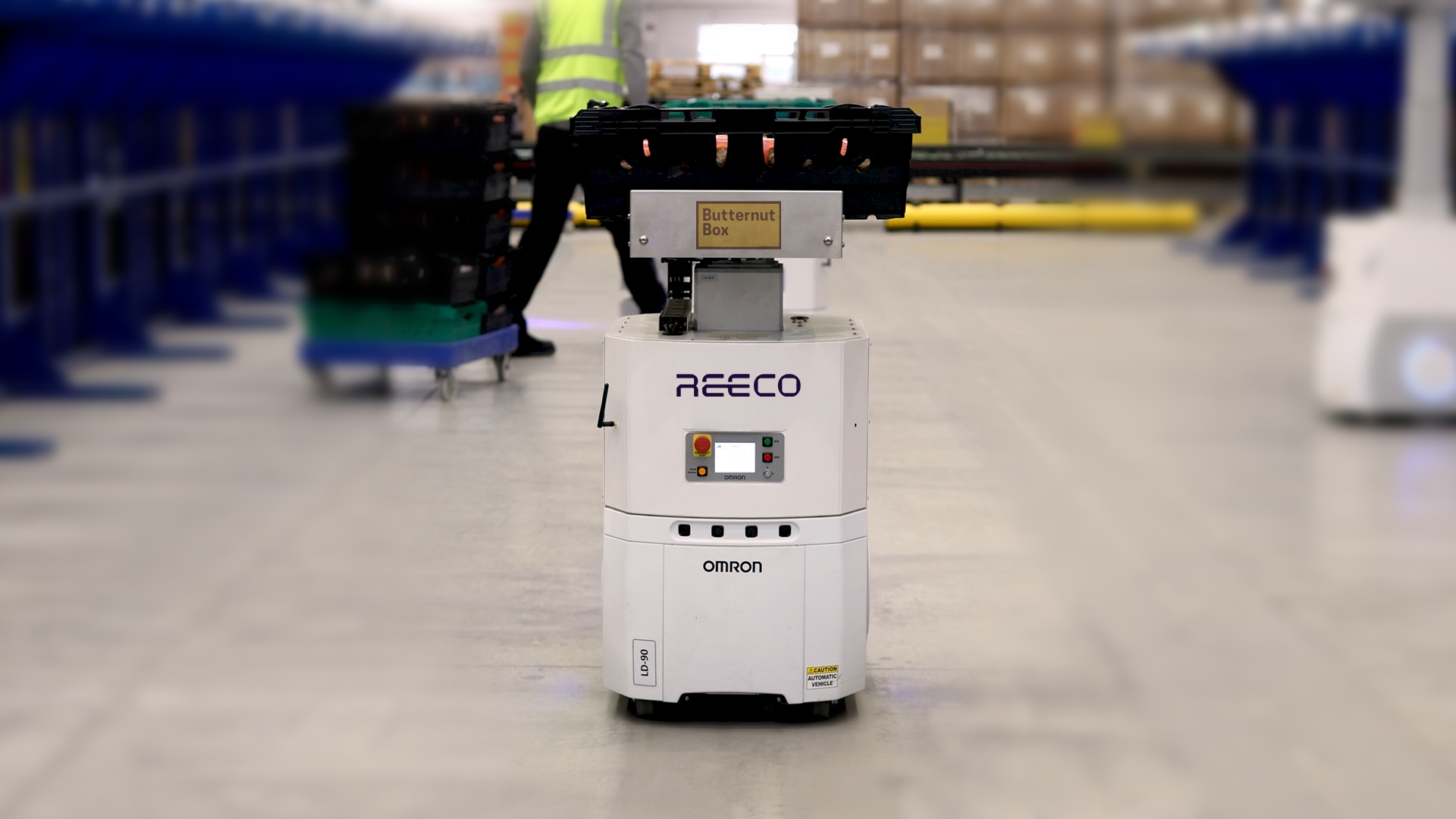
Reeco has recently successfully delivered a fully customised depalletising and product transfer solution to meet fulfilment needs at fresh dog food company Butternut Box. The implementation of an automated product handling system has helped the growing brand to upscale its capabilities and improve efficiency at its new fulfilment facility.The new solution has also significantly reduced the need for manual handling and enabled the redeployment of staff members onto higher-skilled processes along the fulfilment line...
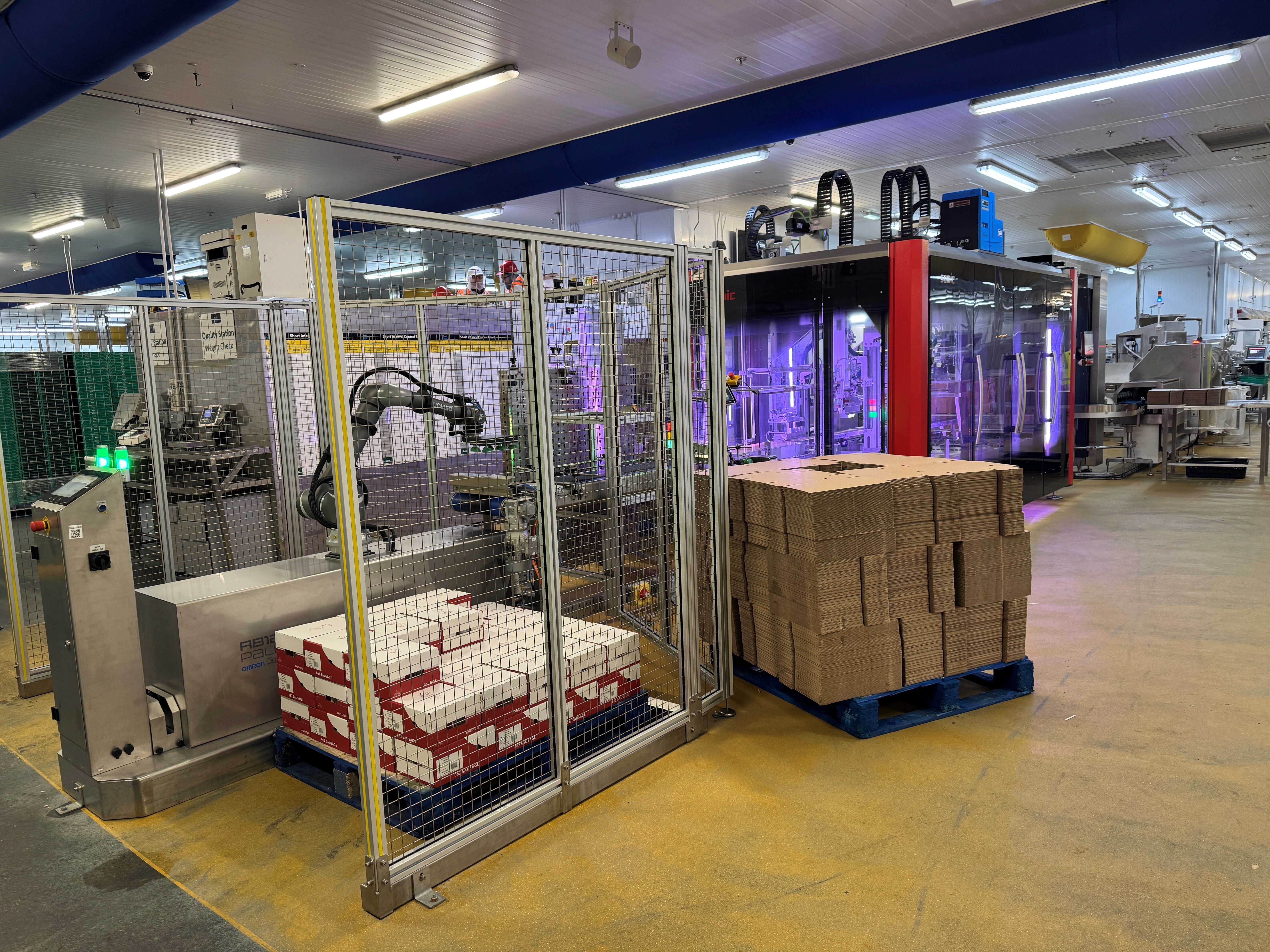
In the face of an increasingly challenging human resource situation in the UK, with manual labour shortages and higher wage bills, more and more businesses are turning towards automation as a reliable way of scaling up. Two companies, Reeco and Somic, have found a perfect synergy delivering automated solutions to end-of-line processes where wraparound packaging is involved. Both are specialists in their own field, delivering innovative high-tech solutions that help businesses to drive cost savings, boost profitability and achieve sustained growth in a challenging economy period.
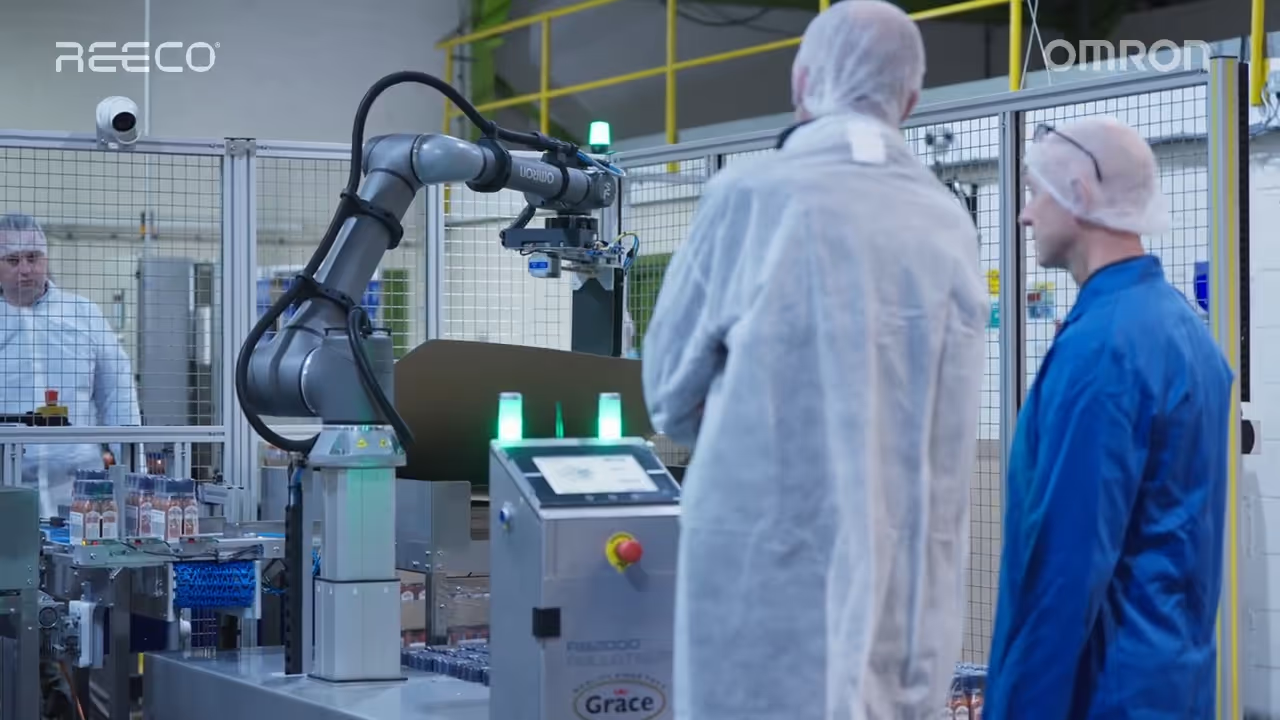
Reeco Automation supplied Grace Foods UK with an RB2000 Palletiser to support its production demands. With a fully-integrated Reeco palletiser, the company has reduced labour at the end of the line by up to 20%, along with increased throughput and reduced downtime.
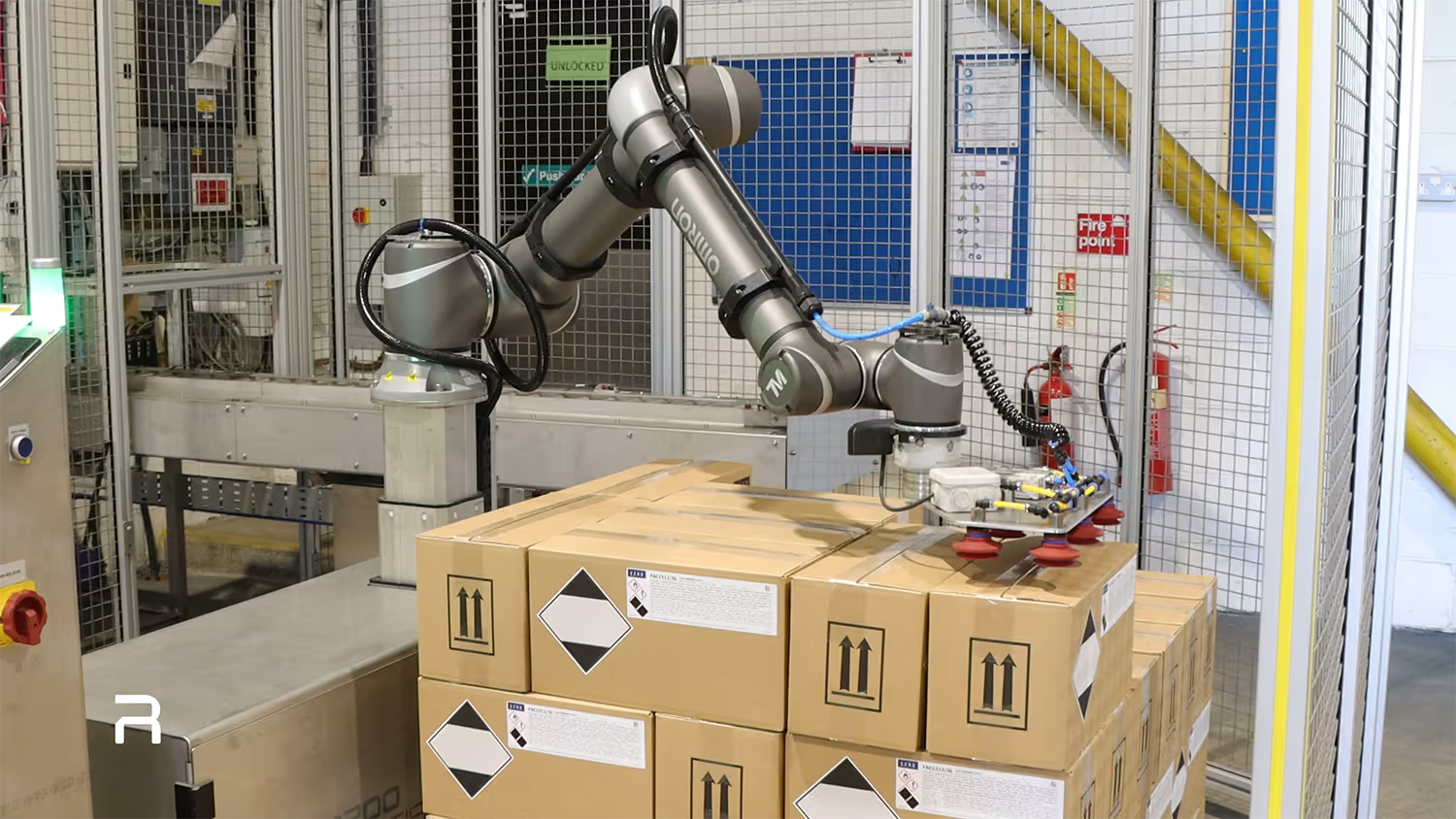
As a specialist integrator of end-of-line automation, we’re renowned for maximising production line efficiency for our customers. Our range of industry-leading products are all designed to work together as a modular system, and in this case study, we uncover how we provided just that for Linx Printing Technologies.
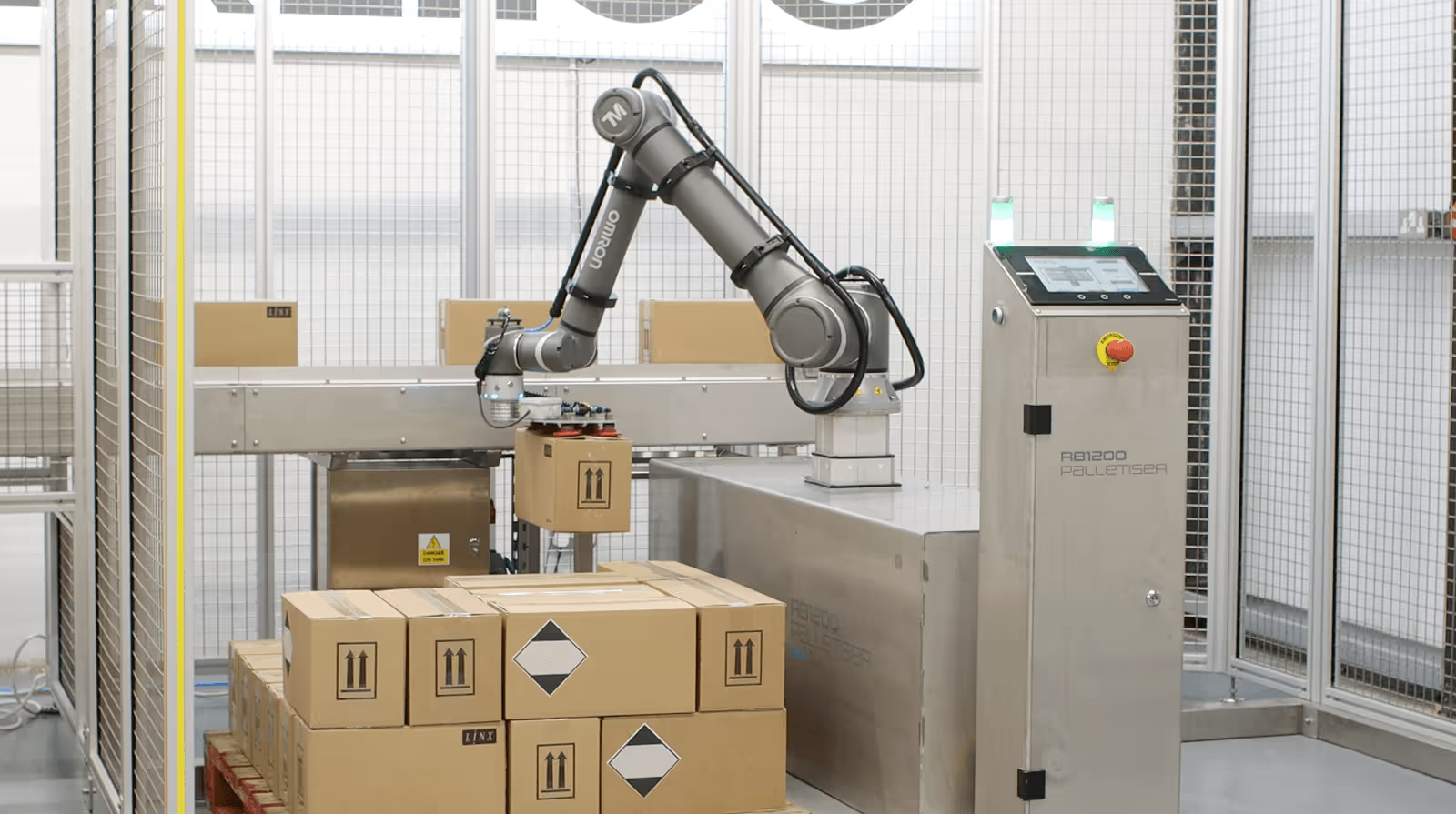
As we look back on five years of our successful partnership with OMRON, we thought it would be good to review how the partnership began and has flourished since. In this article, we tell that story and look specifically at how the two companies came together to build significant market presence with the groundbreaking RB Series Palletiser.
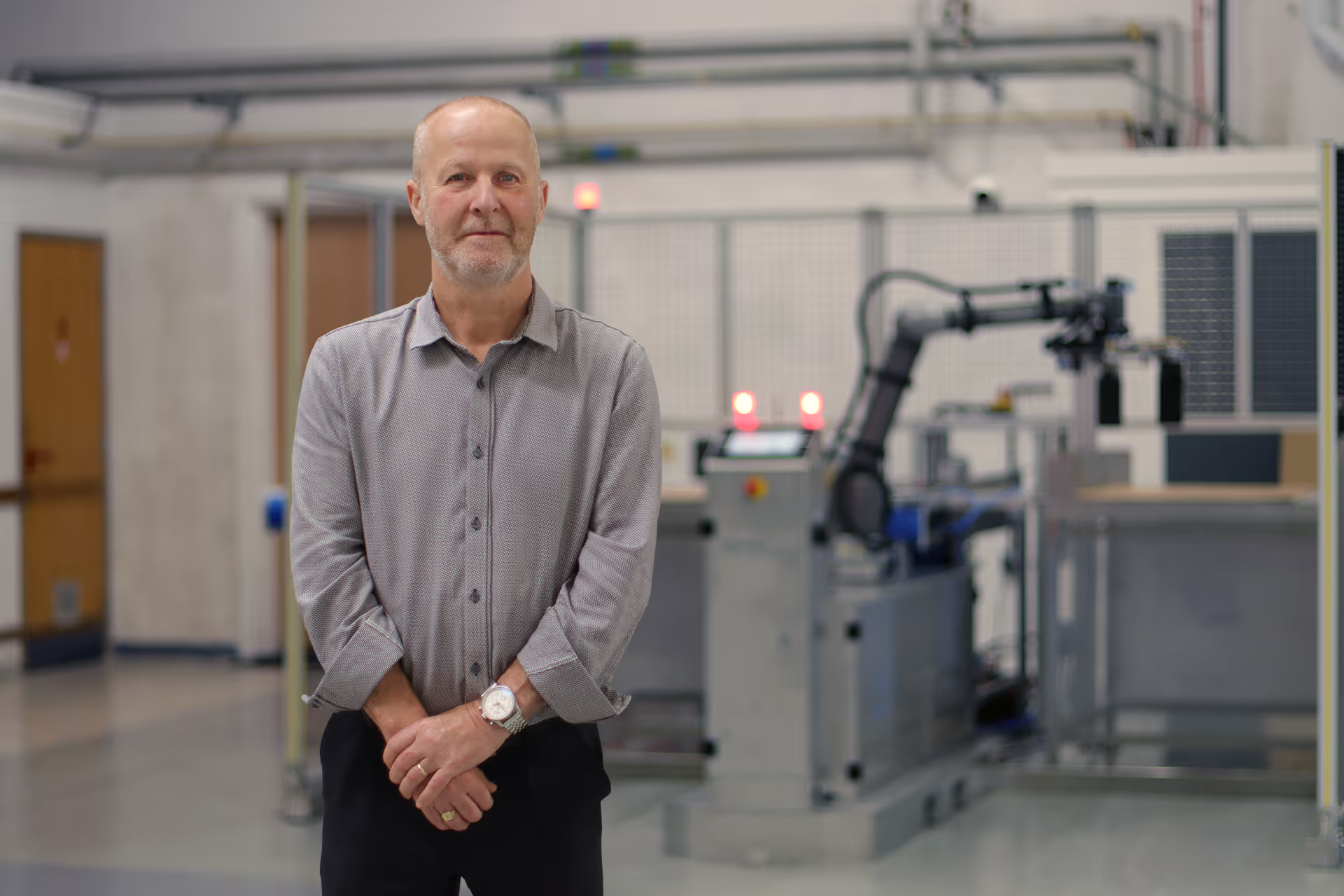
Barry Graham: Technical Sales Manager AMRs
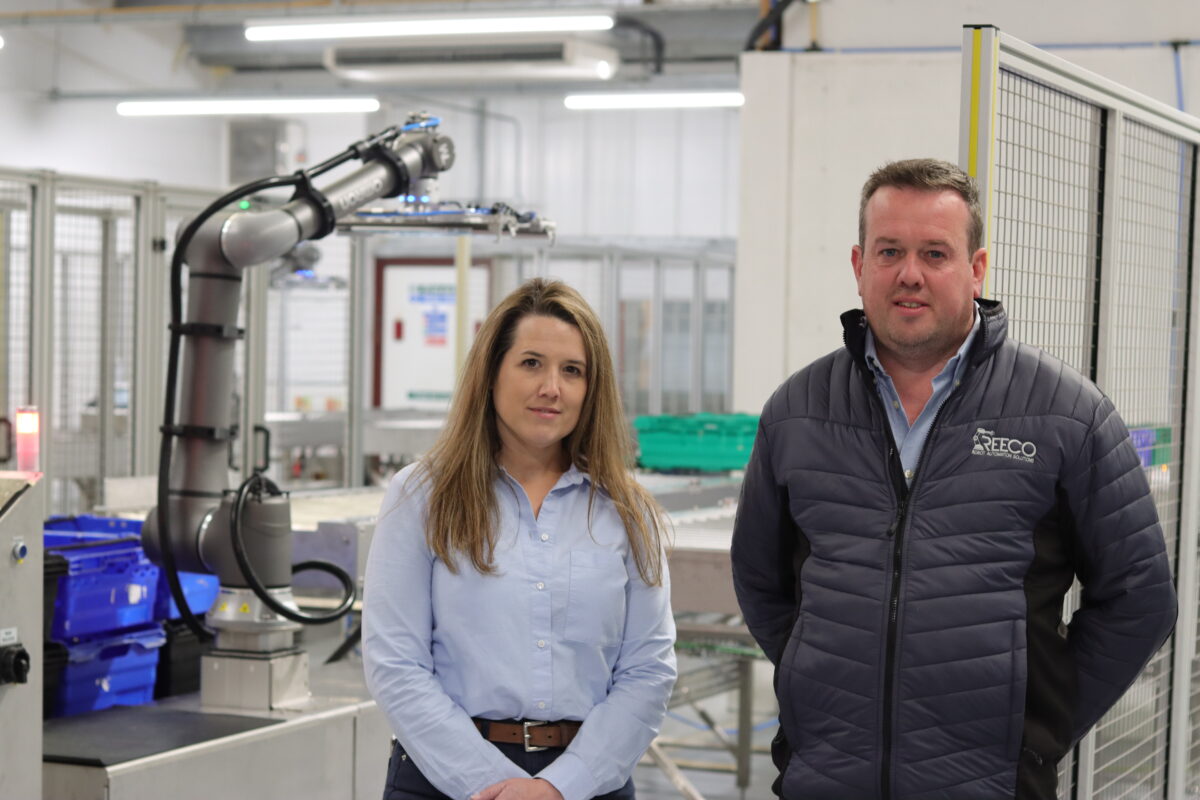
Rosie Davies, Reeco Managing Director (Left) & Llewelyn Rees, Reeco Technical Director (Right)
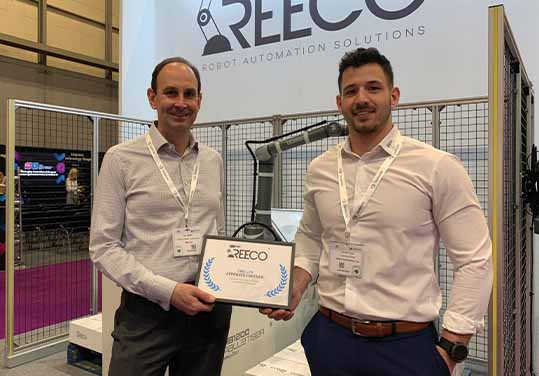
Ian Marks, CME Head of Sales (Left) & Gareth Pugh, Reeco Technical Sales (Right)